Irrigation Management
-
The total water requirement of banana plants is about 900-1200 mm for its entire life cycle and this can be met both through natural precipitation (rainfall) as well as supplementary irrigation.
-
Maintaining optimum moisture at all stages of growth is very critical and providing good drainage facility to drain out excess water from the root zone equally important to promote better growth and enhance the productivity.
-
In general, irrigation of the banana plantations every 3- 4 days during hot period and at 7-8 days interval during cool weather is recommended.
-
In banana plantations different systems of irrigation is in practice and each system has its own merits and demerits. They are
-
Flood or Furrow irrigation, Trench irrigation, Drip Irrigation and Fertigation.
-
Flood or Furrow irrigation is the most common method of irrigation under garden land cultivation. In this system the water consumption is very high and is costly, with uneven distribution of water and fertilizers. There is a chance for fast spread of nematodes
-
Trench irrigation is a popular method of irrigation under wet land system of cultivation where in the water is allowed to stand in the trenches opened between every two rows of plants and the same is used for draining out the excess water during rainy days.
Top of page
Drip irrigation is the method of applying uniform and precise amount of water directly to the root zone of the plants as per the requirement,through emitters at frequent intervals over a long period of time,via a low-pressure pipe network comprising of mains,submains and laterals.
In this system water is applied drop by drop or by micro jet,on the soil surface or below it(sub-surfece),at a rate lower than the infiltration of the soil.
Principles:
Drip irrigation is the most scientific method of irrigation which has the following features:
-
Water is applied at a low rate to maintain optimum air-water balance within the root zone.
-
Water is applied overt a long period of time drop by drop.
-
Water is applied daily at frequent intervals as per the water requirement of plants.
-
Water is applied via a low pressure piping system.
-
Water is supplied to the plants and not to the entire field.
-
The soil moisture content is always maintained at ‘Field Capacity’ of the soil and hence the crops grow at a faster rate consistently and uniformly.
Top of page
|
Components
Head Equipments
-
Water source subsurface tank
-
Pump
-
Filters
Distribution System
-
Mainline
-
Submains
-
Laterals
-
Emitters / Drippers
Head Equipments
Water source subsurface tank :
-
To minimise the energy requirement and also to get a uniform or constant level of water in the effective hydraulic drip irrigation system, it is necessary to construct a subsurface tank in an elevation point at the centre.
-
The capacity of the tank is calculated from the water requirement of the crop, dripper capacity, type of soil etc.
|
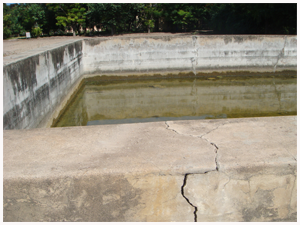 |
Pump:
Filters
1) Gravel or Media Filter:
Media filters consist of fine gravel or coarse quartz sand, of selected sizes (usually 1.5 – 4 mm in diameter) free of calcium carbonate placed in a cylindrical tank. These filters are effective in
removing light suspended materials, such as algae and other organic materials, fine sand and silt
particles. |
2) Screen Filters:
Screen filters are always installed for final filtration as an additional safeguard against clogging.
While majority of impurities are filtered by sand filter, minutes and particles and other small impurities pass through it. The screen filter, containing screen strainer, which filters physical impurities and allows only clean water to enter into the micro irrigationsystem. |
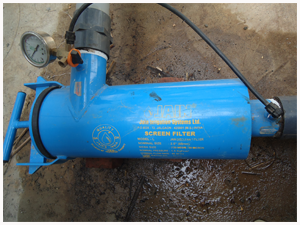 |
3) Centrifugal filters
Centrifugal filters are effective in filtering sand, fine gravel and other high density materials from well or river water.
Water is introduced tangentially at the of a cone and creates a circular motion resulting in a centrifugal force, which throws the heavy suspended particles against the walls.
The separated particles are collected in the narrow collecting vessel at the bottom. |
4) Disk Filters
Disk filter contains stacks of grooved, ring shaped disks that capture debris and are very effective in the filtration of organic material and algae.
During the filtration mode, the disks are pressed together.
There is an angle in the alignment of two adjacent disks, resulting in cavities of varying size and partly turbulent flow. The sizes of the groove determine the filtration grade. Disk filters are available in a wide size range (25 - 400 microns).
Back flushing can clean disk filters. |
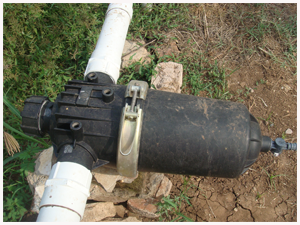 |
Distribution System:
Mainline
The mainline transports water within the field and distribute to submains.
Mainline is made of rigid PVC and High Density Polyethylene(HDPE).
Pipelines of 65 mm diameter and above with a pressure rating 4 to 6 kg/cm2 are used for main pipes. |
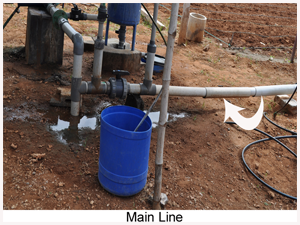 |
Submains:
Submains distribute water evenly to a number of lateral lines.
For sub main pipes, rigid PVC, HDPE or LDPE (Low Density Polyethylene) of diameter ranging from 32 mm to 75 mm having pressure rating of 2.5 kg/cm2 are used. |
Laterals :
Laterals distribute the water uniformly along their length by means of drippers or emitters.
These are normally manufactured from LDPE and LLDPE.
Generally pipes having 10, 12 and 16 mm internal diameter with wall thickness varying from 1 to 3 mm are used as laterals. |
Emitters / Drippers:
They function as energy dissipaters, reducing the inlet pressure head (0.5 to 1.5 atmospheres) to zero atmospheres at the outlet.
The commonly used drippers are online pressure compensating or online non-pressure compensating, in-line dripper, adjustable discharge type drippers, vortex type drippers and micro tubing of 1 to 4 mm diameter.
These are manufactured from Poly- propylene or LLDPE.
Top of page
|
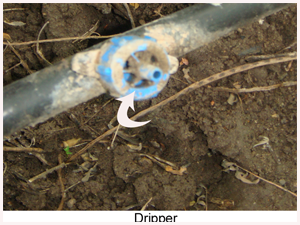 |
Installation of Head Equipments
The following points should be considered for fixing the position of filtern station
-
Minimum use of fitting such as elbows and bends to be made.
-
Whether the pump delivery can be connected to the sand / screen filter
-
Sand / screen filter can easily be connected to mainline
-
Arrangement of back-wash to be made as per the farmer's suitability
-
Arrangement of by-pass water to be made.
-
Sufficient space to be provided for the easy operation of filter valves
-
Hard surface or cement concrete foundation to be made for sand filter so that it will not collapse due to vibration and load. For screen filter provide strong support by using GI fittings to avoid its vibrations due to load.
-
Use hold-tight over the threads of GI fittings and apply proper mixture of M-seal over the joints uniformly to avoid leakage
-
Fix the pressure gauges in inlet and outlet of the filter.
-
Avoid direct linking of oil pump delivery and filter. Instead connect the filter to the pump delivery using flanges or even the hose pipe can be used for this.
|
Connecting Mains And Sub mains:
-
It should be laid at a depth of more than 30 - 45 cm so as to avoid damages during intercultivation
-
Remove mud, if any, in the pipes before fitting. These pipes can be fitted using solvent cement with the help of brush
-
A gunmetal gate valve / PP Ball valve is provided at the start of sub main with PVC MTA fittings for connecting the valve in the PVC sub main
-
Provide flush valve at the end of main and sub main such that it faces towards slope
-
Apply uniform pressure vertically over the drill while drilling in the sub main so that the hole will be smooth and round.
-
Fix the rubber grommets in the holes made in the sub main in such a way that the groove in it goes inside the pipe
-
Fix the take-off position such that its arrow or the chamber faces towards the gate valve of the sub main for the easy flow of water. See that the take-off is fixed tightly in the grommet. The loose fitting of take- indicates the breakage of grommet
-
Get the sub main flushed so that the PVC piece / mud fallen in the sub main while making drill will get flushed. Otherwise this scrap will block the drippers through polytube.
|
Laying of Laterals and drippers:
-
Pass water through the poly tube and get it flushed so that it gets bulged and makes easy for punching
-
Punch the lateral sideway from the yellow strip
-
The dripper position should be fixed according to design, soil and water report and water level in peak summer
-
If two drippers are to be provided such that all the drippers come in a straight line
-
Do not fix drippers unless a complete lateral line is punched. Otherwise the placement of drippers will be changed if moved
-
Punching should be done from the sub main
-
While fixing the dripper, push it inside the lateral and pull it slightly
-
Close the end of lateral by fitting end cap.
|
Month |
Water Req. Lit/Day/Plant |
Month |
Water Req. Lit/Day/Plant |
June |
5-6 |
October |
4-6 |
July |
4-5 |
November |
4-6 |
August |
5-6 |
December |
4-6 |
September |
6-8 |
January |
8-10 |
October |
10-12 |
Febraury |
10-12 |
November |
8-10 |
March |
16-18 |
December |
6-8 |
April |
18-20 |
January |
10-12 |
May |
20-22 |
Febraury |
12-14 |
June |
20-22 |
March |
16-18 |
July |
10-12 |
April |
20-22 |
August |
12-14 |
May |
25-30 |
September |
14-16 |
Area |
1 ha, planting geometry:2m*2m |
Fixed cost of drip system |
Rs.60,700 |
Area interest rate |
10.5% |
Life of system |
7.5 years |
Annual cost of drip |
Rs.17,456 |
Cost of cultivation |
Rs.30,000 |
Expected yield |
47 t/ha |
Expected benefit cost ratio |
4.5 |
12 mm Lateral Pipe - Rs. 3.75/m.
16 mm Lateral Pipe - Rs. 5.80/m.
2 inch Pipe - Rs. 186.00/ 6 m.
1 ¼ inch Pipe - Rs. 112.00/ 6 m.
12 mm start, washer and end cap - Rs. 4.50/ 1 set.
16 mm start, washer and end cap - Rs. 6.80/ 1 set.
Emitter 4 lph, 8 lph, 16 lph - Rs. 2.80 each.
12 mm connector - Rs. 1.00 each.
16 mm connector - Rs. 1.50 each. |
Dummy - Rs. 0.30 each
2 inch Venturi with accessories - Rs. 2000 each.
1 ¼ inch Ball valve - Rs. 120 each.
2 inch Ball valve - Rs. 180 each.
2 ½ inch Ball valve - Rs. 250 each.
5 HP motor pump set - Rs. 10000 each
Screen Filter – 2 inch size - Rs. 2500 each.
Erection charges: Banana - Rs. 0.5 per tree. |
S.No |
Problems |
Causes |
Remedies |
1. |
Leakage of water at the joint between sub main and lateral |
Damaged joints. |
Correct damages. |
2. |
Leakage in the poly tube. |
Damage of polytube by farming activities/rat. |
Block the holes by goof plug. use poly joiners at cuts. |
3. |
Water not flowing upto lateral end. |
Holes in laterals. cuts in laterals. bents in laterals. |
Close the holes and cuts. remove the bends. |
4. |
Out coming of white mixture on removing the end plug. |
More salinity in water. uncleaned lateral. |
Remove the end stop. clean the laterals fortnightly. |
5. |
Under flow or over flow from laterals. |
Clogging of drippers. unclosed end plug. |
Clean the sand and screen filters. close the end cap. |
6. |
Oily gum material comes out on opening the lateral end. |
More algae or ferrous material in water. |
Clean the laterals with water or give chemical treatment. |
7. |
More pressure drop in filters |
Accumulation of dirt in filters |
Clean filters every week. Back wash the filters for every 5 minutes daily. |
8. |
Pressure gauge not working. |
Rain water entry inside. corrosion in gauge pointer damage. |
Provide plastic cover and fix pointer properly. |
9. |
Drop in pressure |
Leakage in main opened outlet. low water level in well. |
Arrest the leakege and close outlet. lower the pump with reference to well water level. |
10. |
More pressure at the entry of sand filter. |
No bypass in the pipeline/bypass not opened. displacement of filter element. less quantity of sand in filters. |
Provide bypass before filter and regulate pressure. place filter element properly. fill required quantity of sand. |
11. |
Accumulation of sand and debris in screen filter |
Displacement of filter element.Less quantity of sand in filters. |
Place filter element prpoperly.Fill required quantity of sand |
12. |
Ventury not working during chemical tratment and fertigation |
Excess pressure on filters improper fitting of ventury assembly |
Bypass extra water to reduce pressure repair the ventury assembly |
13. |
Leakage of water from air release valve |
Damaged air release valve ring |
Replace the damaged ring |
Merits:
-
Increase in yield minimum by 50 60%
-
Quality Improvement of Produce.
-
45 to 50% saving water.
-
Early harvest
-
Uniformity of water application.
-
Precision Placement of Water and Fertilizer.
-
25 to 30% saving fertilizer.
-
Saving in time, labour, energy.
-
Discourages weed Growth.
-
Light soils can be brought under cultivation
-
Soil salinity problem get minimized.
Top of page
|
Demerits
-
Clogging of drippers.
-
Chemical(precipitation)
-
Salt accumulation at wetting front
|
Fertigation
-
Fertigation is the process of applying fertilizers through irrigation system.
-
Fertigation gives flexibility in application of fertilizers, which enables to meet the specific crop requirements at a various stages of growth.
-
Easily and completely soluble nitrogen and potassium fertlisers feeding at the rate of 150 g per plant is sufficient to meet the Nitrogen and Potassium requirement of the crop.
-
Application of Nitrogen in the form of urea and potassium in the form of muriate of potash through the system could be advantageous.
-
These fertilizers could be allowed into the system after making a fertilizer solution in the tank.
-
The fertilizers may be supplied into the system either on daily basis or weekly basis and it may be stopped 10-15 days prior to banana harvest.
-
Apart from the straight fertilizers, there are several formulations of water soluble fertilizers available in the market.
-
A specific formulation needed for banana crop based on the crop growth stage can also chosed for fertigation.
|
WATER SOLUBLE FERTILIZERS (WSF):
Water Soluble Fertilizers are fully water-soluble solid fertilizers having high content of primary nutrients with low salt index. They may or may not have Secondary/micro-nutrients. These water-soluble fertilizers can be advantageously utilized for foliar feeding and Nutrigation / fertigation, thus helping in precision agriculture. |
Choice of fertilizers:
Element |
Fertilizer |
Limitation |
Nitrogen |
Liquid Ammonium nitrate |
None |
Ammonium sulphate |
To be avoided in uses of water having Ca > 70 ppm |
Urea |
None |
Phosphorus |
Super phosphate water |
Colloidal particles well screened
pH of water regulated |
Phosphoric acid |
Very dilute solution
pH regulated
Avoid micronutrient deficiency in the soils |
Potassium |
Liquid potassium nitrate |
None |
|
Liquid potassium chloride |
Avoid when water contain high chloride >300 ppm |
Iron, Zinc |
Chelated compound |
none |
Top of page
Fertilization
-
-
-
Nitrogen Fertilization
-
Nitrogen (N) being one of the major plant nutrients, is often supplied in order to obtain optimum crop production.
-
Nitrogen availability is usually limited in the soil compared with other plant nutrients because its various forms can be leached, volatilized, denitrified or fixed in the organic fraction of the soil.
-
Although water quality must be considered when N is applied through a trickle irrigation system, it is less of a problem than other nutrients such as phosphorus.
-
The injections of anhydrous ammonia or aqua ammonia into irrigation water will bring about an increase of pH that may be conducive to the precipitation of calcium, magnesium and phosphorus, or the formation of complex magnesium ammonium phosphates, which are insoluble. This can be especially serious if bicarbonate is also present in the irrigation water.
-
Nitrogen injected in the form of ammonium phosphate can cause serious clogging of the irrigation system.
-
If calcium and magnesium are present in the irrigation water, the phosphate can form complex precipitates.
-
One of the favoured forms of N for use in this system is urea, because it is a highly soluble nitrogen fertiliser that does not react with water to form ions unless the enzyme urease is present.
-
The enzyme, however, is often found in water containing large amounts of algae or other microorganisms. Since urease is not removed by filtration, its presence could cause hydrolysis of nitrogen in urea to the ammonium ion.
|
PHOSPHORUS FERTILISATION
-
Generally, injection of phosphorus (P) fertiliser through a trickle irrigation system has not been recommended.
-
Most P fertilisers have created chemical or physical precipitation problems and subsequent clogging of the trickle irrigation system.
-
Further, the fixation rate of P by soils is high and subsequent movement from its point of placement is limited.
|
WATER QUALITY INTERACTION WITH P
-
The possibility of precipitation of insoluble phosphate is extremely high in calcium and magnesium.
-
The result is the clogging of emitters or trickle lines with calcium and/or 12 magnesium phosphates.
-
However, if precautions are taken phosphoric or sulphuric acid can be added to a trickle irrigation system to prevent such problems.
|
POTASSIUM FERTILIZATION
-
No adverse chemical reactions are expected with the COl1unon potassium (K) fertilisers when they are added alone to water.
-
However reduced solubility and/or fertiliser incompatibility is possible when different fertiliser types are mixed.
-
An example is a mixture of calcium nitrate and potassium sulphate, which will yield insoluble calcium sulphate.
Top of page
|
Fertigation Scheduling
General Weekly Fertigation Schedule for Banana (g/ plant / application)
Weeks after Planting |
Urea |
Total (g/plant) |
MOP |
Total (g/plant) |
9 to 18 week(10 weeks) |
15 |
150 |
8.0 |
80 |
19 to 30 week(12 weeks) |
10 |
120 |
10 |
120 |
31 to 40 week(10 weeks) |
7.0 |
70 |
12 |
120 |
41 to 46 week(5 weeks) |
Nil |
Nil |
10 |
50 |
Total |
---- |
340 |
---- |
375 |
Schedule of application of fertilizers through drip for Banana
Total quantity of fertilizer required per acre.
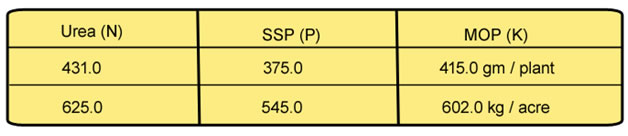
Schedule of solid fertilizer
Water Soluble Solid Fertilizer :
Schedule For Water Soluble Solid Fertilizer
Fertigation schedule for banana variety grand naine
Recommended dose: 200:35:300 g NPK per plant
100 % of TRD as WSF: 635: 111.13: 953 Kg N: P: K per ha
Spacing: 1.5 X 2.1 m (3175 plants per ha)
Sl. No. |
Crop Stage |
Duration |
Fertilizer grade |
Total fertilizer
(Kg per ha) |
1 |
Establishment stage |
9 -18 weeks(10 weeks) |
13-0-45
Urea |
423.13
294.04 |
2 |
Vegetative stage |
19 – 30 weeks(12 weeks) |
13-0-45
Urea |
846.26
450.50 |
3 |
Shooting stage |
31 - 42 weeks(12 weeks) |
Urea
0:0:50 |
275.60
609.92 |
4 |
Development and harvesting stage |
43 - 45 weeks(3 weeks) |
0:0:50 |
152.48 |
P- applied as basal at second month after planting as SSP 111.13 x 6.25 = 695 kg per ha
Fertigation schedule for banana variety- Poovan, Robuta and Dwarf Cavendish
Recommended dose: 100:35:330 g NPK per plant 100 % of TRD as WSF: 317.5:1047.75 Kg N: K per ha .Spacing: 1.5 X 2.1 m (3175 plants per ha)
Sl. No. |
Crop Stage |
Duration |
Fertilizer grade |
Total fertilizer (Kg per ha) |
1 |
Establishment stage |
9 -18 weeks(10 weeks) |
13- 0- 45
Urea |
465.20
75.45 |
2 |
Vegetative stage |
19 – 30 weeks(12 weeks) |
13- 0- 45
Urea |
930.40
82.00 |
3 |
Shooting stage |
31 - 42 weeks(12 weeks) |
Urea
0:0:50 |
137.80
670.56 |
4 |
Development and harvesting stage |
43 - 45 weeks(3 weeks) |
0:0:50 |
167.64 |
‘P- applied as basal at second month after planting as SSP 111.13 x 6.25 = 695 kg per ha
Fertigation schedule for banana variety Nendran
Recommended dose: 150:90:300 g NPK per plant 100 % of TRD as WSF: 476.25: 953.00 Kg N: K per ha. Spacing: 1.5 X 2.1 m (3175 plants per ha)
Sl. No. |
Crop Stage |
Duration |
Fertilizer grade |
Total fertilizer (Kg per ha) |
1 |
Establishment stage |
9 -18 weeks(10 weeks) |
13 -0- 45
Urea |
423.13
190.69 |
2 |
Vegetative stage |
19 – 30 weeks (12 weeks) |
13- 0- 45
Urea |
846.26
278.02 |
3 |
Shooting stage |
31 - 42 weeks(12 weeks) |
Urea
0:0:50 |
609.92
206.69 |
4 |
Development and harvesting stage |
43 - 45 weeks(3 weeks) |
0:0:50 |
152.48 |
‘P- applied as basal at second month after planting as SSP 90 X 317 X 6.25 = 1785.94 kg per ha
Top of page
Fertigation Methods
Methods of fertigation:
Injection of fertilizer and other agrochemicals such as herbicides and pesticides into the drip irrigation system is done by
-
By-pass pressure tank
-
Venturi system and
-
Direct injection system.
(i) By-pass pressure tank:
-
This method employs a tank into which the dry or liquid fertilizers kept. The tank is connected to the main irrigation line by means of a by-pass so that some of the irrigation water flows through the tank and dilutes the fertilizer solution.
-
This by-pass flow is brought about by a pressure gradient between the entrance and exit of the tank, created by a permanent constriction in the line or by a control valve.
|
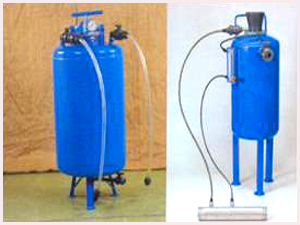 |
(ii) Venturi Injector:
-
A constriction in the main water flow pipe increases the water flow velocity thereby causing a pressure differential (vacuum) which is sufficient to suck fertilizer solution from an open reservoir into the water stream.
-
The rate of injection can be regulated by means of valves. This is a simple and relatively inexpensive method of fertilizer application.
|
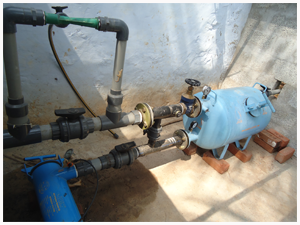 |
(iii) Direct injection system:
-
In this method a pump is used to inject fertilizer solution into the irrigation line. The type of pump used is dependent on the power source.
-
The pump may be driven by an internal combustion engine, an electric motor or hydraulic pressure.
-
The electric pump can be automatically controlled and is thus the most convenient to use. However its use is limited by the availability of electrical power.
-
The use of a hydraulic pump, driven by the water pressure of the irrigation system, avoids this limitation.
-
The injection rate of fertilizer solution is proportional to the flow of water in the system.
-
A high degree of control over the injection rate is possible, no serious head loss occurs and operating cost is low.
-
Another advantage of using hydraulic pump for fertigation is that if the flow of water stops in the irrigation system, fertilizer injection also automatically stops. This is the most perfect equipment for accurate fertigation.
-
Two injection points should be provided, one before and one after the filter for fertigation.
-
This arrangement helps in by-passing the filter if filtering is not required and thus avoids corrosion damage to the valves, filters and filter-screens or to the sand media of sand filters.
-
The capacity of the injection system depends on the concentration, rate and frequency of application of fertilizer solution.
Top of page
|
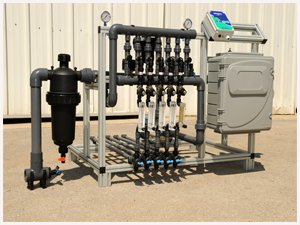 |
Water soluble fertilizers can be injected through
-
Ventury Injector
-
Fertilizer Tank
-
Injector Pump
-
Automatic Fertigation Controller
-
External energy driven injector pumps
Ventury Injector
This is very simple and low cost device. A partial vacuum is created in the system which allows suction of the fertilizers into the irrigation system through a constriction which increase the velocity of flow thus creating a drop in pressure. When the pressure drops the fertilizer solution is sucked into the ventury through a suction pipe from the tank and from the enters into irrigation stream. Although simple and with greater uniformity of dosing than fertilizer tank the ventury cause a high pressure loss in the system which may result in uneven water & fertilizer distribution in the field. The suction rate of ventury is 30 to 120 lit. per hour. |
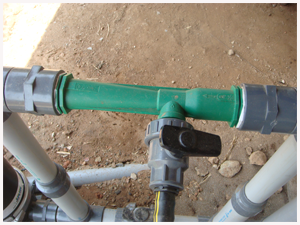 |
Fertilizer Tank
In this system part of irrigation water is diverted from the main line to flow through a tank containing the fertilizer in a fluid or soluble solid form, before returning to the main line, the pressure in the tank and the main line is the same but a slight drip in pressure is created between the off take and return pipes for the tank by means of pressure reducing valve. This causes water from main line to flow through the tank causing dilution and flow of the diluted fertilizer into the irrigation stream. With this system the concentration of the fertilizer entering the irrigation water charges continuously with the time, starting at high concentration. As a result uniformity of fertilizer distribution can be problem. Fertilizer tanks are available in 90,120,160 liters capacity. |
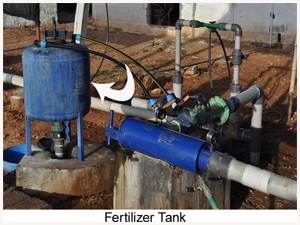 |
Fertilizer Injector Pump
These are piston or diaphragm pumps which are driven by the water pressure of the irrigation system and such as the injection rate is proportional to the low of water in the system. A high degree of control over the fertilizer injection rate is possible, no serious head losses are incurred and operating cost are low. Another advantage is that if the flow of water stops. Fertilizer infection also automatically stops. This is perfect equipment for accurate fertigation. Suction rates of pumps varies from 40 lit to 160 lit per hour. |
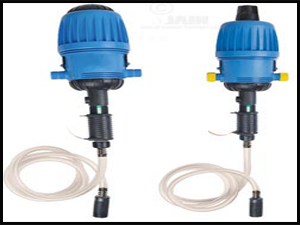 |
Automatic Fertigation Controller
Automatic fertigation control system are installed for proper fertilization controlling. the following are the advantages of installing an automatic system:
-
It gives proper proportionate and timely fertigation to the crop
-
It helps save fertilizers upto 20%
-
It increasing the yield upto 10-15%
-
Easy installation
-
Controls pH & EC or pH & TDS
-
No peristaltic pumps
-
Industrial grade probes
-
Less maintenance stays in calibration longer
-
Works with any type of hydrophonic system
|
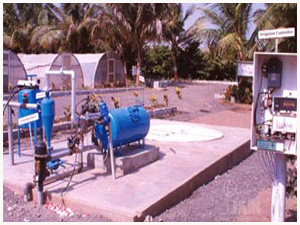 |
CRITERIA FOR APPLYING FERTILISERS
-
All chemicals applied through irrigation systems must meet the following criteria. They must
-
(i) avoid corrosion, softening of plastic pipe tubing, or clogging of any component of the system
-
(ii) be safe for field use
-
(iii) increase or at least not decrease crop yield
-
(iv) be soluble or emulsifiable in water and
-
(v) not react adversely to salts or other chemicals in the irrigation water.
-
In addition, the chemicals or fertiliser must be distributed uniformly throughout the field. Achieving such uniformity of distribution requires efficient mixing, uniform water application, knowledge of the flow, characteristics of water and fertilisers in the distribution lines.
-
To avoid clogging, chemicals applied through drip irrigation system must meet certain requirements.
-
The chemicals must be completely soluble. If more than one material is used in preparing a concentrated stock solution for subsequent injection into the drip lines the chemicals must not react with each other to form a precipitate.
-
The chemicals must also be compatible with the salts contained in the irrigation water.
-
The injection points should be provided, one before and one after the filter.
-
This arrangement can be used to bypass the filter if filtering is not required, and thus avoid corrosion damage to the valves, filters, and filter screens or to the sand media of sand filters.
-
Furthermore, the discharge line from the fertiliser tank should have a filter, and similarly, the injection hoses line should be equipped with an in line hose filter or screen.
-
The intake or suction side of tile injector should be equipped with a filter or strainer.
-
Injection points must be installed so that injected fertilisers are properly mixed before the flow divides in several directions.
-
The size of capacity of the injection system depends on the concentration, rate and frequency of application.
-
Naturally, less fertiliser solution and more frequent application require smaller, less costly units.
-
Fertiliser application rates and application times vary considerably depending on crop and emitter spacing.
|
Merits
-
Increase in yield minimum by 25-30%
-
Export quality production
-
Saving in fertilizers by 25-30%
-
Precise application of fertilizers
-
Uniform distribution of fertilizers
-
Nutrient requirements can be fulfilled as per physiological stages
-
Acidic nature helps to neutralize salts in water & soil
-
Acidic nature helps in avoiding clogging of drippers, it cleans drip system
-
No nutrient loss by leaching, fixation & volatilization
-
Major & micro nutrients can be applied in one solution
-
Fertilizers can be injected as per required concentration
-
Improve efficiency of fertilizer & water
-
Saving in time, labour, energy
-
Light soils can be brought under cultivation
|
Demerits
-
Toxicity to field workers
-
Chance of backflow into water source, for that NRV and vacuum valve has to be installed
-
Insoluble fel1ilisers are not suitable (super phosphate)
-
Corrosive effect of fertiliser
-
Phosphate may get precipitated in the pipe line and dripper due to pH reaction
-
High cost
|
Top of page